"Wij zijn goed begeleid bij de overgang naar een nieuw ERP-systeem; een risicovol traject."
ELCEE is een leverancier van mechanische industriële componenten en samenstellingen, zowel standaard als geëngineerd. Bedrijfsonderdelen bevinden zich onder meer in Nederland, Duitsland en Zweden. Ook in Azië is ELCEE actief, en dan met name in China waar veel inkoopactiviteiten plaatsvinden. Als dominante speler in een gefragmenteerde markt werden verschillende acquisities gedaan, niet alleen in de al genoemde Europese landen, maar ook in België, Denemarken en Polen. Door de overnames, maar ook door organische groei, steeg de omzet in drie jaar tijd van circa veertig naar meer dan honderd miljoen euro. Na deze snelle groei wilde industriële leverancier ELCEE de informatieprocessen samenbrengen en optimaliseren.
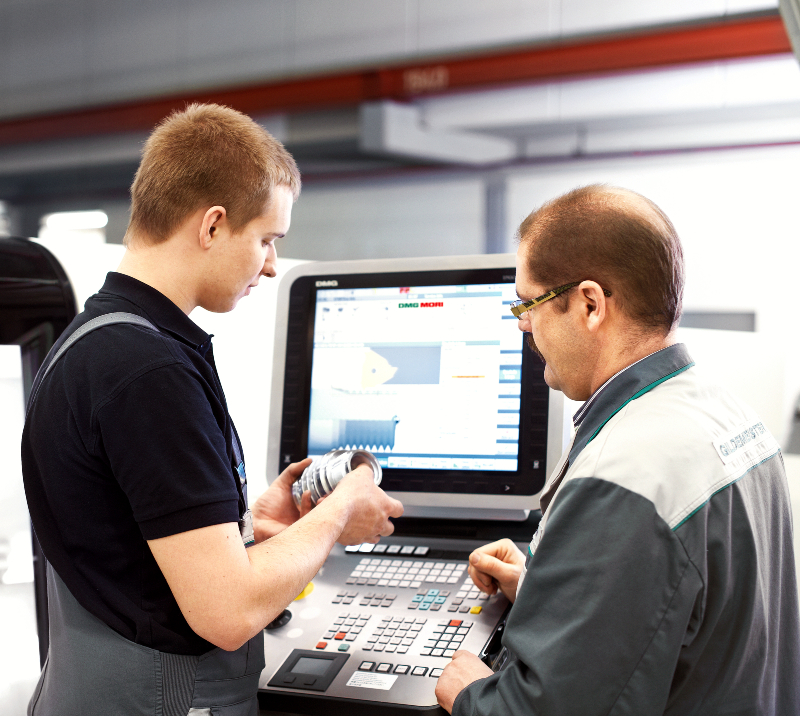
Eén ERP voor de hele onderneming
Het voordeel van al deze overname activiteiten is dat de organisatie nu de schaalgrootte en slagkracht heeft om op Europees niveau te concurreren. Tegelijkertijd bracht de integratie van verschillende kleinere bedrijven met de hoofdorganisatie de nodige groeistuipen. “Allemaal hadden ze hun eigen manier van werken en ook hun eigen ERP-pakket”, zegt Richard Meeuwissen, COO van Elcee Group B.V. Anderhalf jaar geleden begon Richard bij ELCEE met als opdracht het optimaliseren van alle logistieke en informatieprocessen voor de gehele ELCEE groep. Als onderdeel van dit project deed Skopos de procesanalyse, stelde een blauwdruk op en begeleidde de selectie van een leverancier, alsmede de contractering voor de aanschaf van een nieuw systeem.
Knelpunten in kaart gebracht
“Waar wij naar op zoek gingen was financiële consolidering, een beter inzicht in kerncijfers, zoals die van onze sales, en het verbeteren van onze productiviteit. Maar ook het stroomlijnen van warehouse logistics en de inkoopactiviteiten waren voor ons belangrijk”, zegt Meeuwissen. “De grote wens voor de hele onderneming was: één ERP-pakket, maar om daar te komen, moesten we eerst een inventarisatie maken van de systemen en werkprocessen in onze ELCEE groep om uit te vinden waar de bottlenecks zich bevonden. Ook wilden we een ERP-blauwdruk laten maken om onze kritische processen en informatiebehoeften, niet alleen in het heden, maar ook voor de toekomst, vast te leggen.”
“Wat ons aansprak bij Skopos was hun hands-on mentaliteit. Dit maakt complexe materie toegankelijk, zowel wat betreft de software als het change management.” Vooral dat laatste aspect wordt bij de overgang naar een nieuw ERP-systeem wel eens onderschat door bedrijven, weet Meeuwissen. “Je hebt nu eenmaal te maken met kerngebruikers die een bepaald systeem gewend zijn. Bij de overgang naar een nieuw systeem is het belangrijk dat deze gebruikers de juiste aandacht krijgen.”
Aandacht voor kerngebruikers
Tijdens het traject vonden enkele verschuivingen plaats. Zo werd aanvankelijk nog het behoud van het huidige systeem niet uitgesloten, maar in de procesanalysefase kwamen Skopos en ELCEE al snel tot de conclusie dat het niet mogelijk was het huidige systeem voldoende aan te passen. Gilde Buy Out Partners, dat als investeringsmaatschappij halverwege het traject een belang nam in ELCEE, gaf de beslissende zet richting de implementatie van een nieuw pakket. “Zij hechten grote waarde aan één systeem waarin actuele cijfers op ieder moment zijn op te vragen. Zij zagen dit als voorwaarde om als bedrijf de volgende stap te kunnen zetten.” Consultancybedrijf PWC voerde een audit uit op het project. “Zij oordeelden positief over hoe wij het traject hebben aangevlogen, evenals de support die wij daarbij kregen van Skopos.”
Minstens zo belangrijk als de kennis en kunde die Skopos inbracht, was de spiegel die Meeuwissen en zijn collega’s regelmatig voorgehouden kreeg. “Skopos stelde kritische vragen, bijvoorbeeld waarom wij processen op een bepaalde manier organiseerden of waarom er bepaalde configuraties waren gemaakt.” De groep kerngebruikers werd ook voortdurend meegenomen in het proces. “Op de juiste momenten werd de groep ingeschakeld, zodat wij konden evalueren waar we stonden en waar eventuele risico’s en angsten zaten. Jan-Willem Ruessink, die het traject namens Skopos begeleidde, voelde dit met zijn kennis van verandermanagement telkens haarfijn aan. Dit hebben wij als zeer prettig ervaren.”
Juiste focus en planning
Het traject van procesanalyse tot het contracteren van de gekozen leverancier heeft in totaal acht maanden geduurd. Een traject waarop Meeuwissen tevreden terugkrijgt. “Het heeft de juiste focus en planning gekregen om te komen tot waar we nu staan. Je praat over een grote investering en een risicovol traject, daarin zijn wij keurig begeleid.” Parallel aan het maken van de blauwdruk stelde Skopos met ELCEE een longlist van ERP-leveranciers op, welke in een later stadium werd teruggebracht tot een shortlist met twee leveranciers. Deze werden uitgenodigd voor demosessies, waarbij nauwkeurig is gekeken of de geboden oplossing aansloot bij de, in de blauwdruk, geschetste behoeften.”
Skopos voerde na de selectie ook de onderhandelingen met de gekozen leverancier. “Belangrijk, vindt Meeuwissen, want een ERP-implementatie is iets waarin bedrijven doorgaans weinig ervaring kunnen opbouwen. Dit doe je als organisatie misschien eens in de tien jaar. De ervaring die Ruud Haring van Skopos op dit gebied inbracht, is daarom van grote waarde voor ons geweest. Niet alleen in de laatste fase, maar tijdens het gehele traject heeft Skopos zich als dienstverlener telkens flexibel en proactief opgesteld tijdens alle vraagstukken die er optraden”, stelt Meeuwissen. Veelzeggend vindt hij het advies dat zijn organisatie kreeg om te investeren in kennis en kunde op het gebied van supply chain management. “Dit heeft ertoe geleid dat wij ons personeel binnen de organisatie op verschillende plekken hebben versterkt, waardoor wij nu ook op eigen kracht de implementatie van het pakket uit kunnen voeren. Skopos heeft zichzelf hiermee eigenlijk overbodig gemaakt, wat ik alleen maar zeer positief vind. Dit betekent dat er echt vanuit de klant is gedacht.”
Goed gevoel
Inmiddels is de kick-off van de implementatie achter de rug. “Het traject met Skopos is twee maanden geleden, op een zeer prettige manier, gezamenlijk afgerond. Nu is het aan ons om de implementatie uit te voeren. Wij hebben een goed gevoel bij het gekozen pakket, een beeld dat verder is versterkt na enkele referentiebezoeken bij andere bedrijven. Dat gaf vertrouwen.” Het doel is om in oktober de implementatie af te ronden. “We gaan een systeem krijgen waarmee we onze processen en productiviteit gaan verbeteren, maar ook beter met Business Intelligence en actuele management KPI’s kunnen monitoren. Daarmee is de basis gelegd voor verdere groei in onze markt.”
Ook verder groeien met een goede basis?
Wij kunnen je daarbij helpen. Neem gerust contact op om eens vrijblijvend te sparren. Dat kan via onderstaande knop. Laat je gegevens achter en we nemen zo spoedig mogelijk contact met je op.
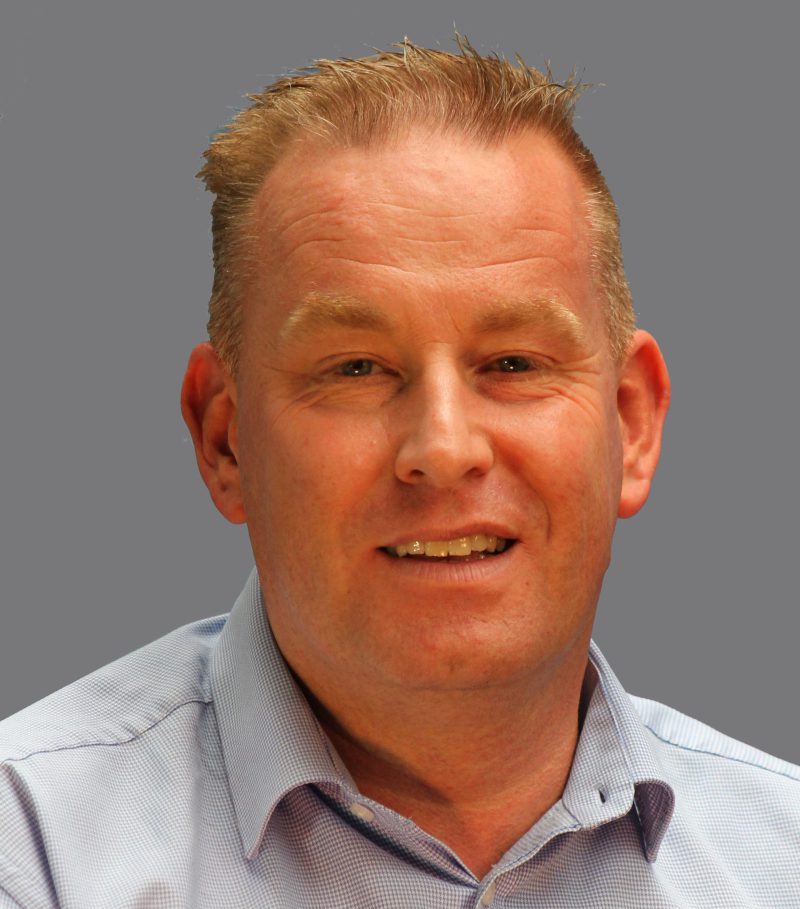